Air Pollution Control Equipment’s
In the industrial operations the handling of dry process materials like minerals, products, food grains etc. generates dust by virtue of fall, collision and storage, which creates dust pollution in the atmosphere causing health hazard to the human being (workers), loss of materials. Hence it is mandatory by the regulatory authority to control these dust by various air cleaning.
Air cleaning devices remove contaminates from an air or gas stream. They are available in a wide range of designs to meet variations in air cleaning requirements. Degree of removal required, quantity and characteristics of the contaminant to be removed and conditions of the air or gas stream will all have a bearing on the device selected for any given application.
Dust Collector – Dust collection equipment is available in numerous designs utilizing many different principles and featuring wide variations in effectiveness, operating maintenance cost, space, arrangement and materials of construction.
There are four major types of dust collectors for particulate contaminants are:
- Electrostatic precipitators.
- Fabric collectors.
- Wet collectors.
- Dry centrifugal collectors.
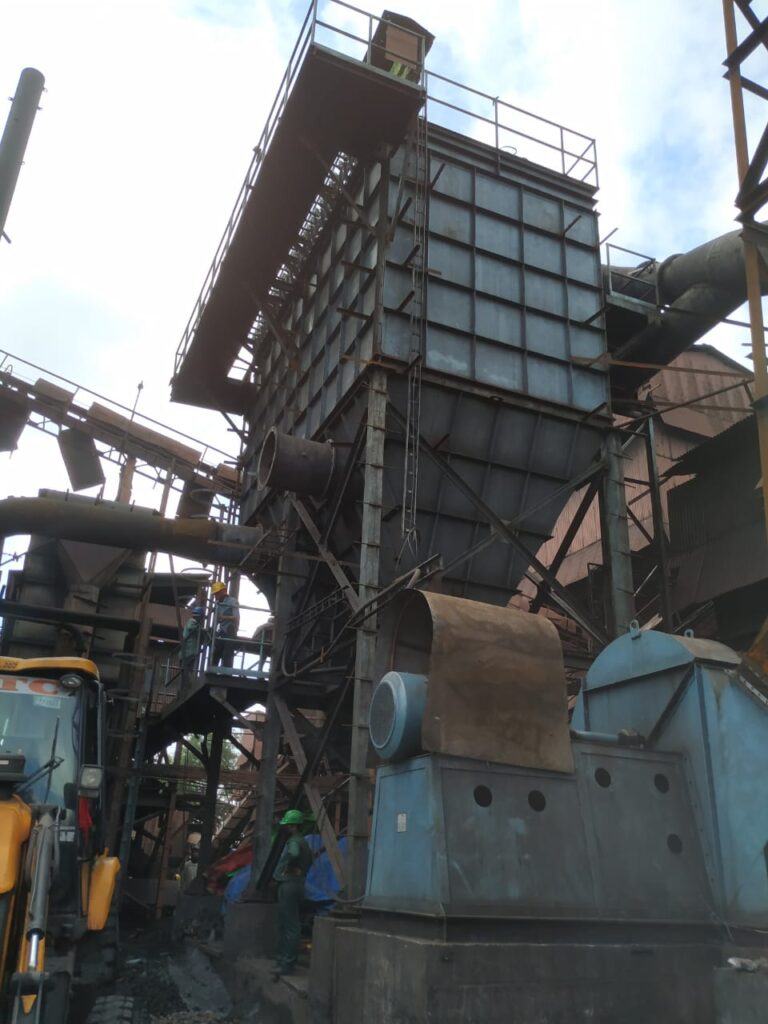
Electrostatic Precipitators:
Electrostatic precipitator are generally use for removal of ash in the flue gas stream of power plants cold fire boilers.
Refer different page for the details about Electrostatic Precipitator.
Fabric Filters/Bag House Filter :
Fabric collectors remove particulate by straining, impingement, interception, and diffusion and electrostatic charge. The fabric may be constructed of any fibrous material, either natural or man-made, and may be spun into a yarn and woven or felted by needling, impacting, or bonding. Woven fabrics are identified by thread count and weight per unit area. Regardless of construction, the fabric represents a porous mass through which the gas is passed unidirectional such that dust particles are retained on the dirty side and the cleaned gas passes on through. The ability of the fabric to pass air is stated as “permeability” and is defined as the cubic feet of air passed through one square foot of fabric each minute at a pressure drop of 0.5″wg. Typical permeability values for commonly used fabrics range from 25 to 40 cfm.
The design of an industrial baghouse involves consideration of many factors including space restriction, cleaning method, fabric construction, fiber, air-to-cloth ration and many construction details such as inlet location, hopper design and dust discharge devices.
Fabric collectors are sized to provide a sufficient area of filter media to allow operation without excessive pressure drop. The amount of filter area required depends on many fact’s, including:
- Release characteristics of dust.
- Porosity of dust cake
- Concentration of dust in carrier gas stream.
- Type of fabric and surface finish, if any.
- Type of reconditioning.
- Reconditioning interval
- Air flow pattern within collector
- Temperature and humidity of gas stream.
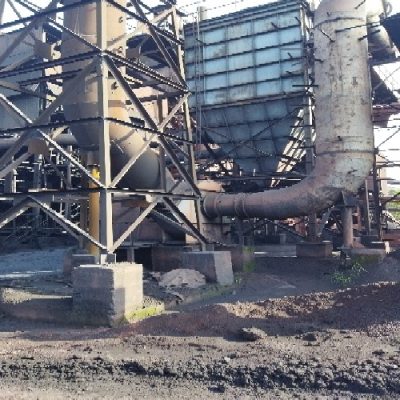

Scrubbers:
Some of the most commonly used air pollution control devices in manufacturing and processing facilities, industrial air scrubbers employ a physical process—i.e., scrubbing—which removes particulates and gases from industrial emissions, such as smokestack exhaust (in the case of exhaust air scrubbers), before they are released into the atmosphere. There are two main categories of scrubbers—dry scrubbers and wet scrubbers.
Dry Scrubbers :
- Particle size, weight and shape. Performance is improved as size and weight become larger and as the shape becomes more spherical.
- Collector size and design. The collection of fine dust with a mechanical device requires equipment designed to best utilize mechanical forces and fit specific application needs.
- Velocity, pressure drop through a cyclone collector increases approximately as the square of the inlet velocity. There is however an optimum velocity that is a function of collector design, dust characteristics, gas temperature and density.
- Dust concentration generally the performance of a mechanical collector increases as the concentration of dust becomes greater.
Dry scrubbers, also referred to as dry adsorption scrubbers, inject dry neutralizing chemical agents, such as sodium bicarbonate, into the emission stream, causing the gaseous pollutants contained within to undergo a chemical reaction which either neutralizes the pollutants or converts them into innocuous substances. Once the chemical reaction concludes, filters within the scrubber chamber collect and remove the spent agents from the cleaned emission gas. In some cases, the collected agents can be washed and reused for future dry scrubbing processes, but, if not possible, the scrubbing waste must be disposed of by specialists. Typically, dry scrubbers are used to remove or counteract acid gas within industrial emissions. The chemical reactions resulting from the addition of neutralizing agents during the dry scrubbing process helps to both reduce the acidity of the emissions and remove air pollutants.
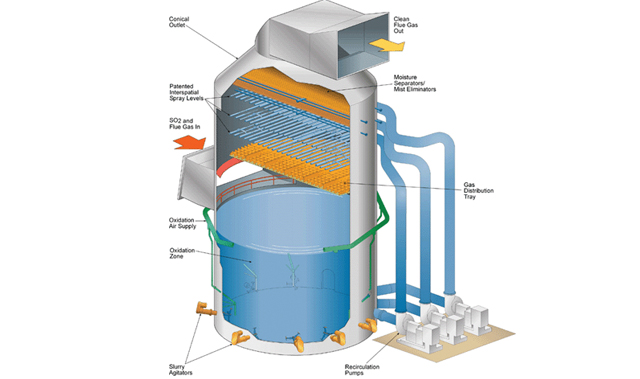
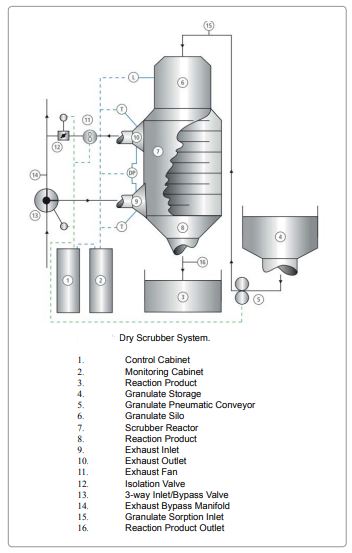
Wet Scrubbers :
Wet scrubbers, also referred to as wet adsorption scrubbers or wet collectors, employ liquid solutions—typically water—to collect and remove water-soluble gas and particulate pollutants from industrial emissions. The wet scrubbing process either passes a gas stream through a liquid solution or injects a liquid solution into a gas stream. As the gas stream comes into contact with the liquid, the solution absorbs the pollutant removing it from the stream. The types of wet scrubbing equipment available include venturi, packed bed (or packed tower), and bubbling scrubbers.
FGD- Flue Gas Desulphurization:
Macon Enviro provides FGD (Flue Gas Desulphurization) System for the following Industries.
- Coal Fired Boilers & Power Plants.
- Pet Coke Fired Boilers & Furnaces.
- High Capacity DG sets.
All types of Flue Gas Desulphurization (FGD) plants are custom designed by Macon Enviro Engineers by their & technology partner’s long experience in the field of FGD & Air Pollution Control systems.
Depending upon the availability of re-agent like Lime, limestone, sea water, alkali, Flue Gas Desulphurization system can be designed in most economical manner and systems are provided to utilize the system waste to useful products like sulphuric acid & Gypsum to recover cost incurred in Opex. Macon’s Engineers contributed vital roll in FGD installation for coal fired power plant cumulative approx 2500 MW & other furnaces up to 5 lacs m3 of flue gas volume.
Macon has a strong & reputed vendor base for indigenous and imported equipments like RC Pumps, Gas to Gas Heater, Booster Fan, Vaccum Belt Filter, Flue Gas Dampers etc. Macon has also well capable Fabricators & Erectors for quality execution of FGD units who have experience of execution of many FGD erection work.
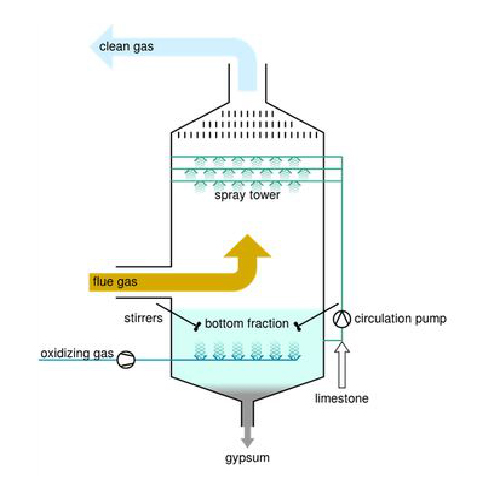